Flaw Testing, flawlessly done
The Cyl-Sonic Digital Industrial System scans through paint and most clear coatings to detect potential pits, cracks, corrosion and gouges. In addition, the system measures and detects lost cylinder wall thickness as well as identifies undesirable moisture inside the cylinders
Wheel Probe Technology
The ultrasonic wheel probe includes nine complementary high-frequency transducers - the most integrated transducers in one unit in the industry - that search for flaws in traverse, longitudinal and oblique directions. This ensures 100% coverage of required exam volume and area. The four oblique transducers excel in detecting any moisture droplets inside cylinders.
Safer to Operators and Environment
Unlike hydrostatic testing methods, ultrasonic examination eliminates the need to remove hazardous gases from cylinders, helping protect both your operators and the environment. The method does not require valve or O-ring removal, so there is less need for valve replacement as well as reduced cylinder neck thread damage.
Ultrasonic examination also eliminates the need to introduce water into the cylinders, helping prevent product contamination and elimination or minimizing the number of post-re-qualification cylinder treatment processing steps.
One Machine, Many Cylinder Types
The Cyl-Sonic Industrial system handles a wide range of outside diameters, lengths and materials which means you can inspect most cylinder types using a single machine. A built in calibration cylinder stage, which can be configured to the left or right side of the machine, allows for automated and efficient cal-in and cal-out procedures.
Saves Time, Lower Costs and Productivity through Automation
The Cyl-Sonic Industrial saves on personnel costs. Since operators don’t need to spend time drying and re-valving the cylinders, daily production levels can be much higher. The cost per cylinder test is lower for UE testing than hydrostatic testing.
To meet your high-volume, high-productivity needs, the system includes optional decks or tables that allow staging and simultaneous loading/unloading of cylinders while the automated testing process continuously operates. Pneumatically operated up-enders and down-enders assist with the handling of large cylinders.
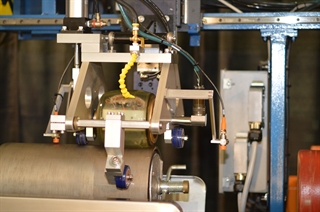
Calibration Standards ensure Accuracy
Each system uses calibration cylinder standards with simulated flaws. This allows accurate comparison testing against known simulated flaws.
Software control and record retention
The Cyl-Sonic Cylinder Test application has been updated to support Nordco’s high definition, digital control electronics. The software allows the operator to control all axis motion, including position, rotation, and sensitivity. Calibration setups are stored and reused. The software displays real-time scanning test results showing the locations of any detected flaws; the system also alerts the operator about a cylinder’s pass/fail status.
Ideal for integration with other processes
The Cyl-Sonic Industrial can be easily customized to integrate with any or all of the following operational processes:
-
Database Bar-coding
-
Surface blasting
-
Painting
-
Marking
Meets all regulatory requirements
The Cyl-Sonic Industrial complies with the requirements of the following regulatory agencies:
-
DOT - Meets US Department of Transportation cylinder re-qualification requirements (SP 14920)
-
TC - Meets Transport Canada cylinder re-qualification requirements (SU 10807)
-
ISO - Meets International organization for Standardization requirements (ISO 10461 & 6406)
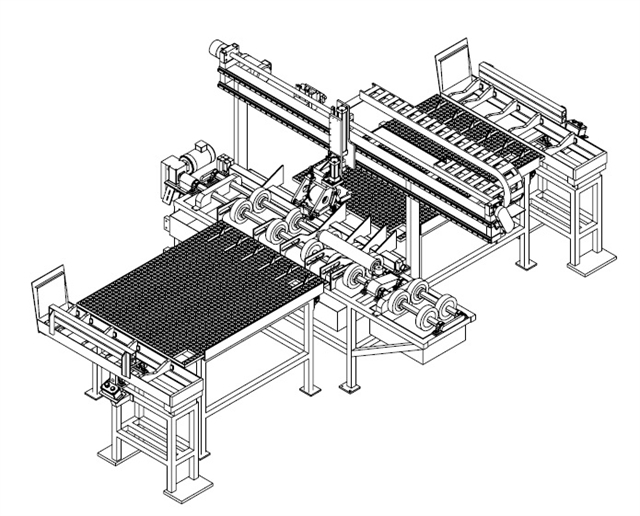
Specifications
General |
|
Length |
10’ 10” (3302 mm) |
Width |
3’ 10” (1168 mm) |
Height |
7’ 1” (2159 mm) |
Weight |
~4600 lbs (2087 kg), includes control cabinet but no cylinder table |
|
|
Cylinder Inspection |
|
Product to be tested
|
- Steel (DOT 3A and 3AA)
- Aluminum (DOT 3AL)
- other exception steel cylinders per USDOT and ISO 4606 & 10461 specifications
|
Diameter Range |
4” to 10” (102 mm to 267 mm) outside diamete |
Wall Thickness |
0.080” to 1.0” (2 mm to 25.4 mm) |
Length |
11” to 72” (279 mm to 1524 mm) |
Exam Coverage |
110% with a 0.25” (6 mm) helix |
System Performance |
98%+ System Uptime |
|
|
Utilities |
|
Electric |
220/110 VAC, 60 Hz, 25A |
Pneumatic |
100 psi (6.9 bar) |
Estimated System Throughput |
Cylinder Model |
Outside Diameter |
Length w/o Valve/Cap |
Estimated Throughput |
300 (3AA) |
9.25" |
55" |
27-30 cylinders/hour* |
Medical E (3AL) |
4.3" |
25.75" |
27-30 cylinders/hour* |
20 (3AA) |
5.25" |
14" |
48-60 cylinders/hour* |
* Operator dependent
Standard Configurations and Options
Calibration stage on the right side of the main unit. |
1104401 Load Conveyor - Main Unit - Down Ender
1104402 Up Ender - Inlet Table - Main Unit - Outlet Table - Down Ender
1104403 Up Ender - Main Unit - Down Ender
|
Calibration stage on the leftside of the main unit. |
1104411 Load Conveyor - Main Unit - Down Ender
1104412 Up Ender - Inlet Table - Main Unit - Outlet Table - Down Ender
1104413 Up Ender - Main Unit - Down Ender
|
Optional Equipment |
Length Test Verification: A set of proximity sensors that validate that the cylinder has been tested over its entire length. |
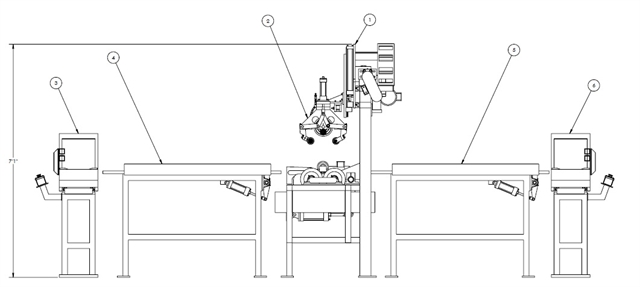
Identifier |
Description |
1 |
Cylinder Testing System Main Unit |
2 |
Industrial Ultrasonic Examination Assembly, Vertical Lift |
3 |
Up Ender, Gas Cylinder |
4 |
Inlet Table 65" (1651 mm) or 18" (457 mm) long |
5 |
Outlet Table 65" (1651 mm) or 18" (457 mm) long |
6 |
Down Ender, Gas Cylinder |